度过最艰难痛苦的一年,特斯拉的未来会好吗?
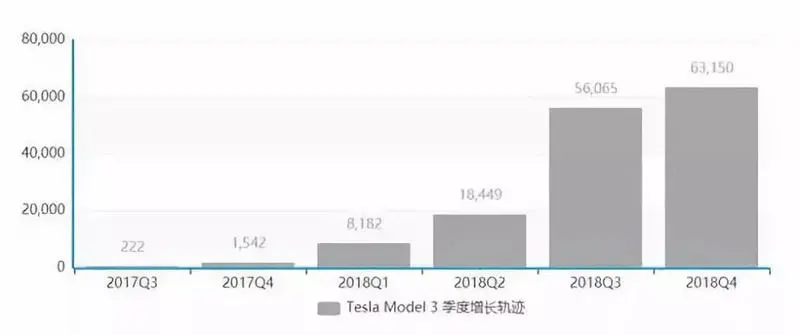
产品魔咒
在过去的 18 个月里,关于Model 3的产能地狱的报道层出不穷,Model 3到底怎么了?
到今天我们能看得比较清晰:Model 3没能跳出特斯拉的产品魔咒,它是Model X之后,特斯拉又一个生死存亡式的硬核挑战。
Roadster:第一款产品,如果特斯拉没能在 2008 年以合理的成本结构实现 Roadster 的产能爬坡和交付,它一定会破产。
Model S:第二款产品,更准确地说,是推动特斯拉从电动跑车制造商向豪华汽车制造商转型的首款产品。如果特斯拉没能在 2012 年以合理的成本结构实现Model S产能爬坡和交付,它一定会破产。
Model X:第三款产品,作为Model S同平台的SUV产品,Model X在特斯拉发展历程中本没有那么关键。
但包括全景式挡风玻璃、双绞链感应式鹰翼门等设计使得Model S/X 的零部件复用率下跌至 30%,Model X成为世界上最难制造的汽车。特斯拉团队遇到的挑战不亚于开发一款全新车型。
那Model 3呢?其实可以对比一下Model X和Model 3的产能爬坡轨迹。
2017 年 7 月,特斯拉交付了首批Model 3,随后电池组产线,四大生产工艺先后陷入产能地狱,直到2018年 Q4,Model 3的产能和交付规模才达到了一个相对稳定的节奏。
如果以上就是特斯拉在2018的全部,故事讲到这里就该结束了。显然,真相比表象呈现得更复杂。
Model 3产能爬坡失败可以给出一个结论:Elon为Model 3设计的产能爬坡计划,基本失败了。
还是前面那两张图,重点在最后两个季度的数据。增幅减小,趋于一致。这意味着特斯拉产能已经能满足当季市场需求,完全解决了Model X的产能问题。
但Model 3不是这样的。到今天为止,特斯拉仍然积压着超过 20 万Model 3订单没能消化,这个时候产能趋于稳定,不是市场需求得到了满足,而是产能爬坡失败了。
Model X作为“世界上最难制造的汽车”,特斯拉花一年时间搞定了它的产能。Model 3到底有多复杂呢?
在2017 年的特斯拉股东大会上,Elon向股东介绍了Model 3的设计逻辑。
整整6 个月,Model 3产能爬坡停滞不前。在特斯拉历史上,这样的困境尚属首次。
事实上,Model 3带给特斯拉的挑战,远甚于Model X。
再激进一些让我们把时间拨回 2015 年,以更深刻的理解,为什么特斯拉的2018会如此艰难。
会议结束后,蓝星项目正式启动(在 2007 年的特斯拉商业计划书中,Elon将“大众可负担得起的轿车项目”命名为蓝星项目)。
最初制定的研发周期是:2015 年 1 月启动,2017 年年底交付。也就是说,Model 3最初制定的研发周期为 35 个月。
就像Elon说的,Model 3是特斯拉最后一次押上整个公司命运的赌注,从一开始,整个公司就在以 All in 的姿态推进Model 3项目。
2015 年 10 月,也就是Model X开始交付一个月后,特斯拉研发部门大多数工程师都从Model X项目撤出,转入Model 3项目组。
一切看起来都在朝着正确的方向前进,但到了 2016 年 5 月,一切都变了。
Elon召开会议宣布,特斯拉将在2018年将产能提升至 50 万辆/年。这比之前的规划提前了 15 个月,比最初的规划提前了 24 个月。为了配合这个新目标,所有的业务进度都得重新调整。
2016 年 5 月,特斯拉围绕Model 3项目做了一大波密集的调整。
首先,Model 3量产节点提前了 4 个月,改为 2017 年 7 月 1 日投产。也就意味着,Model 3的研发周期压缩至 30 个月。
其次,内华达州超级工厂 Gigafactory 1 设定的50 GWh/年产能目标提前至2018年,以配合 50 万辆/年的电池组需求。
第三,加速推进能量密度更高、成本更低的 2170 电池商业化,100美元/kWh 的成本目标由 2020 年提前至2018年实现。
最后,抽调Model 3项目研发团队,组建“Model 3全自动生产线”项目研发团队,由高级工程副总裁 Doug Field 领导。
尽管做了全方位的调整工作和一系列密集的部署,如你所知,Model 3产能爬坡计划,基本失败了。
一个关键的问题是,在一切都有条不紊地向前推进的时候,Elon为什么在 2016 年 5 月决定“再激进一些”?
“无畏舰”2016年 5 月往回拨两个月,特斯拉刚刚发布了智能电动汽车行业的里程碑车型Model 3。
而特斯拉内部最激进的订单预测是 5 万个,换句话说,市场的热情比特斯拉的最乐观预期好了一个数量级。
这种来自全球各地的热情是认可,也是压力。在那之后,Elon的关注点从“如何制造最好的智能电动汽车”变成了“如何制造效率最高、产能爬坡最快的工厂”。
当他的注意力集中在汽车上时,特斯拉造出了Model SP100D 这样的车型;当他认真审视汽车生产线的时候,会发生什么呢?
2016 年 5 月 31 日,特斯拉股东大会上,Elon分享了他对工厂的思考。
在过去的两三个月里,我逐渐意识到生产汽车的改进潜力比汽车工程本身的改进潜力要高十倍。
我们意识到这才是真正的问题、真正的挑战,也是最大的潜力所在。我们正在打造制造机器的机器,要真正把工厂本身视为一款产品、一款相当垂直整合的产品去打造。把工厂中出现的问题更多的看成工程或技术挑战去解决。
相同的占地面积,Dreadnought 的产能将达到传统产线的 10 倍。
毫无疑问,这是科幻片里才有的、高度智能化和自动化的机器人产线才可能实现的场景。但来自Model 3巨大订单压力,让Elon推动特斯拉自动化产线团队在2018年将之落地。
2017 年 11 月的特斯拉 Q3 财报会议上,特斯拉全球销售与服务总裁 Jon McNeill 简单介绍了设计 Dreadnought 的难度。
Dreadnought 有着极其复杂的电气、机械和软件方面的挑战,设计这样的产线和推出一款全新车型的难度没有什么区别。
被高估的机器人,被低估的人类Jon McNeill 错了,实际上,以2018年或者说当今的技术水平,这样的产线根本无法落地。
最终版本的 Dreadnought 由 5 个车间、超过 1000 台制造机器人、0 个工人组成,特斯拉团队设计了数十个子产线来组合成完整的 Dreadnought。
它包括 100% 全自动化的四大工艺产线和一条超级复杂的零部件传送带网络。包括多种传感器、计算机视觉、机器人学、自动化、软件工程、机械、电子电气等多个学科的人才团队参与设计。
特斯拉团队始终无法解决给螺栓穿孔、准确识别并抓取线束、传感器失灵、机器人大量崩溃重启等问题。
最夸张的一次,由于零部件传送带停止工作,100 辆驶下产线的Model 3没有装右大灯。特斯拉最终为这些车型返工装上了大灯,但自动化产线的问题再也无法忽视。
2018年 4 月,Elon对自动化产线改进的期望急转直下,也可以说对所面临的挑战有了更清醒的认识:特斯拉终于拆掉了那条产线。转而推出了新的半自动化、更多人工介入的产线。
Elon第一次公开承认,过度自动化是个错误,确切的说,是我的错误,人类被低估了。
深远的影响产线拆掉了,但推行Model 3产能爬坡计划这件事本身仍然在深刻地影响着特斯拉的发展。
首先是产线本身,很多人对“建起一条产线,将之拆掉”的投入没有概念,更何况是特斯拉这种业内首创的,大量介入研发的全自动产线呢?
20亿美元什么概念呢,特斯拉上海超级工厂 Gigafactory 3 的设计投资额,也就20亿美元。
但问题在于,史无前例的、长期高强度的工作加高强度的压力让Elon变得极度情绪化,典型表现如2018年年中草率发起 & 终止特斯拉私有化、在 Twitter 上与媒体起争执等。
所有管理层都承受着巨大的压力,虽然高管离职在特斯拉早就不算新鲜事,但核心幕僚的离开,仍然在一定程度上影响了特斯拉的发展。
2018年2月,特斯拉全球销售与服务总裁 Jon McNeill 离职
2018年5月,特斯拉高级工程副总裁 Doug Field 宣布休假(随后离职)
这两位高管的 Title 很关键,特斯拉有几十名副总裁或同级别的高管,只有 Jon 去掉了“副”,Doug 则加上了“高级”。
特斯拉没有COO,而 Jon 和 Doug 扮演的就是联席COO的角色,这两位是Elon在特斯拉与下面几十名高管沟通的纽带。
在这两位离职后,所有业务 VP 都改为直接向Elon汇报。2018年 9 月 7日,Elon对特斯拉组织架构进行了彻底的重构,新的管理架构更加极致的扁平化。
前Model S、Semi Truck 和如今Model 3项目负责人 Jerome Guillen 在重组中被提报为汽车业务总裁。
下一个,是因全自动产线走的弯路,导致所有业务及新产品的集体推迟。
你会发现特斯拉的产品组合规划是一环扣一环严丝合缝的,一旦有一个环节掉链子,全盘都要受影响。现在,掉链子的是Model 3未能起量。
未来一片光明现在看来,特斯拉在2018年遇到的一切困境,都源于 2016 年 5 月的激进规划。如果没有 Dreadnought,也就不会有这么多困难和挑战出现了。
有人会说,在传统车企纷纷觉醒的今天,特斯拉失去的不仅是高管和几十亿美元,2018年未能实现 50 万辆/年的产能,以及与之匹配的其他业务进展,丢掉的空窗期才是最大的损失。
对于这个说法,我想贴Elon的传记《硅谷钢铁侠》中的一段话。
别忘了,特斯拉最初的计划是 2020 年实现 50 万辆/年的产能,虽然2018年最终未能实现,但即便推迟到 2019 年,也比原计划提前了整整一年。
让我们把时间拨回 2015 年,以更深刻的理解,为什么特斯拉的2018会如此艰难。
会议结束后,蓝星项目正式启动(在 2007 年的特斯拉商业计划书中,Elon将“大众可负担得起的轿车项目”命名为蓝星项目)。
最初制定的研发周期是:2015 年 1 月启动,2017 年年底交付。也就是说,Model 3最初制定的研发周期为 35 个月。
就像Elon说的,Model 3是特斯拉最后一次押上整个公司命运的赌注,从一开始,整个公司就在以 All in 的姿态推进Model 3项目。
2015 年 10 月,也就是Model X开始交付一个月后,特斯拉研发部门大多数工程师都从Model X项目撤出,转入Model 3项目组。
一切看起来都在朝着正确的方向前进,但到了 2016 年 5 月,一切都变了。
Elon召开会议宣布,特斯拉将在2018年将产能提升至 50 万辆/年。这比之前的规划提前了 15 个月,比最初的规划提前了 24 个月。为了配合这个新目标,所有的业务进度都得重新调整。
2016 年 5 月,特斯拉围绕Model 3项目做了一大波密集的调整。
首先,Model 3量产节点提前了 4 个月,改为 2017 年 7 月 1 日投产。也就意味着,Model 3的研发周期压缩至 30 个月。
其次,内华达州超级工厂 Gigafactory 1 设定的50 GWh/年产能目标提前至2018年,以配合 50 万辆/年的电池组需求。
第三,加速推进能量密度更高、成本更低的 2170 电池商业化,100美元/kWh 的成本目标由 2020 年提前至2018年实现。
最后,抽调Model 3项目研发团队,组建“Model 3全自动生产线”项目研发团队,由高级工程副总裁 Doug Field 领导。
尽管做了全方位的调整工作和一系列密集的部署,如你所知,Model 3产能爬坡计划,基本失败了。
一个关键的问题是,在一切都有条不紊地向前推进的时候,Elon为什么在 2016 年 5 月决定“再激进一些”?
“无畏舰”2016年 5 月往回拨两个月,特斯拉刚刚发布了智能电动汽车行业的里程碑车型Model 3。
而特斯拉内部最激进的订单预测是 5 万个,换句话说,市场的热情比特斯拉的最乐观预期好了一个数量级。
这种来自全球各地的热情是认可,也是压力。在那之后,Elon的关注点从“如何制造最好的智能电动汽车”变成了“如何制造效率最高、产能爬坡最快的工厂”。
当他的注意力集中在汽车上时,特斯拉造出了Model SP100D 这样的车型;当他认真审视汽车生产线的时候,会发生什么呢?
2016 年 5 月 31 日,特斯拉股东大会上,Elon分享了他对工厂的思考。
在过去的两三个月里,我逐渐意识到生产汽车的改进潜力比汽车工程本身的改进潜力要高十倍。
我们意识到这才是真正的问题、真正的挑战,也是最大的潜力所在。我们正在打造制造机器的机器,要真正把工厂本身视为一款产品、一款相当垂直整合的产品去打造。把工厂中出现的问题更多的看成工程或技术挑战去解决。
相同的占地面积,Dreadnought 的产能将达到传统产线的 10 倍。
毫无疑问,这是科幻片里才有的、高度智能化和自动化的机器人产线才可能实现的场景。但来自Model 3巨大订单压力,让Elon推动特斯拉自动化产线团队在2018年将之落地。
2017 年 11 月的特斯拉 Q3 财报会议上,特斯拉全球销售与服务总裁 Jon McNeill 简单介绍了设计 Dreadnought 的难度。
Dreadnought 有着极其复杂的电气、机械和软件方面的挑战,设计这样的产线和推出一款全新车型的难度没有什么区别。
被高估的机器人,被低估的人类Jon McNeill 错了,实际上,以2018年或者说当今的技术水平,这样的产线根本无法落地。
最终版本的 Dreadnought 由 5 个车间、超过 1000 台制造机器人、0 个工人组成,特斯拉团队设计了数十个子产线来组合成完整的 Dreadnought。
它包括 100% 全自动化的四大工艺产线和一条超级复杂的零部件传送带网络。包括多种传感器、计算机视觉、机器人学、自动化、软件工程、机械、电子电气等多个学科的人才团队参与设计。
特斯拉团队始终无法解决给螺栓穿孔、准确识别并抓取线束、传感器失灵、机器人大量崩溃重启等问题。
最夸张的一次,由于零部件传送带停止工作,100 辆驶下产线的Model 3没有装右大灯。特斯拉最终为这些车型返工装上了大灯,但自动化产线的问题再也无法忽视。
2018年 4 月,Elon对自动化产线改进的期望急转直下,也可以说对所面临的挑战有了更清醒的认识:特斯拉终于拆掉了那条产线。转而推出了新的半自动化、更多人工介入的产线。
Elon第一次公开承认,过度自动化是个错误,确切的说,是我的错误,人类被低估了。
深远的影响产线拆掉了,但推行Model 3产能爬坡计划这件事本身仍然在深刻地影响着特斯拉的发展。
首先是产线本身,很多人对“建起一条产线,将之拆掉”的投入没有概念,更何况是特斯拉这种业内首创的,大量介入研发的全自动产线呢?
20亿美元什么概念呢,特斯拉上海超级工厂 Gigafactory 3 的设计投资额,也就20亿美元。
但问题在于,史无前例的、长期高强度的工作加高强度的压力让Elon变得极度情绪化,典型表现如2018年年中草率发起 & 终止特斯拉私有化、在 Twitter 上与媒体起争执等。
所有管理层都承受着巨大的压力,虽然高管离职在特斯拉早就不算新鲜事,但核心幕僚的离开,仍然在一定程度上影响了特斯拉的发展。
2018年2月,特斯拉全球销售与服务总裁 Jon McNeill 离职
2018年5月,特斯拉高级工程副总裁 Doug Field 宣布休假(随后离职)
这两位高管的 Title 很关键,特斯拉有几十名副总裁或同级别的高管,只有 Jon 去掉了“副”,Doug 则加上了“高级”。
特斯拉没有COO,而 Jon 和 Doug 扮演的就是联席COO的角色,这两位是Elon在特斯拉与下面几十名高管沟通的纽带。
在这两位离职后,所有业务 VP 都改为直接向Elon汇报。2018年 9 月 7日,Elon对特斯拉组织架构进行了彻底的重构,新的管理架构更加极致的扁平化。
前Model S、Semi Truck 和如今Model 3项目负责人 Jerome Guillen 在重组中被提报为汽车业务总裁。
下一个,是因全自动产线走的弯路,导致所有业务及新产品的集体推迟。
你会发现特斯拉的产品组合规划是一环扣一环严丝合缝的,一旦有一个环节掉链子,全盘都要受影响。现在,掉链子的是Model 3未能起量。
未来一片光明现在看来,特斯拉在2018年遇到的一切困境,都源于 2016 年 5 月的激进规划。如果没有 Dreadnought,也就不会有这么多困难和挑战出现了。
有人会说,在传统车企纷纷觉醒的今天,特斯拉失去的不仅是高管和几十亿美元,2018年未能实现 50 万辆/年的产能,以及与之匹配的其他业务进展,丢掉的空窗期才是最大的损失。
对于这个说法,我想贴Elon的传记《硅谷钢铁侠》中的一段话。
别忘了,特斯拉最初的计划是 2020 年实现 50 万辆/年的产能,虽然2018年最终未能实现,但即便推迟到 2019 年,也比原计划提前了整整一年。
Jon McNeill 错了,实际上,以2018年或者说当今的技术水平,这样的产线根本无法落地。
最终版本的 Dreadnought 由 5 个车间、超过 1000 台制造机器人、0 个工人组成,特斯拉团队设计了数十个子产线来组合成完整的 Dreadnought。
它包括 100% 全自动化的四大工艺产线和一条超级复杂的零部件传送带网络。包括多种传感器、计算机视觉、机器人学、自动化、软件工程、机械、电子电气等多个学科的人才团队参与设计。
特斯拉团队始终无法解决给螺栓穿孔、准确识别并抓取线束、传感器失灵、机器人大量崩溃重启等问题。
最夸张的一次,由于零部件传送带停止工作,100 辆驶下产线的Model 3没有装右大灯。特斯拉最终为这些车型返工装上了大灯,但自动化产线的问题再也无法忽视。
2018年 4 月,Elon对自动化产线改进的期望急转直下,也可以说对所面临的挑战有了更清醒的认识:特斯拉终于拆掉了那条产线。转而推出了新的半自动化、更多人工介入的产线。
Elon第一次公开承认,过度自动化是个错误,确切的说,是我的错误,人类被低估了。
深远的影响产线拆掉了,但推行Model 3产能爬坡计划这件事本身仍然在深刻地影响着特斯拉的发展。
首先是产线本身,很多人对“建起一条产线,将之拆掉”的投入没有概念,更何况是特斯拉这种业内首创的,大量介入研发的全自动产线呢?
20亿美元什么概念呢,特斯拉上海超级工厂 Gigafactory 3 的设计投资额,也就20亿美元。
但问题在于,史无前例的、长期高强度的工作加高强度的压力让Elon变得极度情绪化,典型表现如2018年年中草率发起 & 终止特斯拉私有化、在 Twitter 上与媒体起争执等。
所有管理层都承受着巨大的压力,虽然高管离职在特斯拉早就不算新鲜事,但核心幕僚的离开,仍然在一定程度上影响了特斯拉的发展。
2018年2月,特斯拉全球销售与服务总裁 Jon McNeill 离职
2018年5月,特斯拉高级工程副总裁 Doug Field 宣布休假(随后离职)
这两位高管的 Title 很关键,特斯拉有几十名副总裁或同级别的高管,只有 Jon 去掉了“副”,Doug 则加上了“高级”。
特斯拉没有COO,而 Jon 和 Doug 扮演的就是联席COO的角色,这两位是Elon在特斯拉与下面几十名高管沟通的纽带。
在这两位离职后,所有业务 VP 都改为直接向Elon汇报。2018年 9 月 7日,Elon对特斯拉组织架构进行了彻底的重构,新的管理架构更加极致的扁平化。
前Model S、Semi Truck 和如今Model 3项目负责人 Jerome Guillen 在重组中被提报为汽车业务总裁。
下一个,是因全自动产线走的弯路,导致所有业务及新产品的集体推迟。
你会发现特斯拉的产品组合规划是一环扣一环严丝合缝的,一旦有一个环节掉链子,全盘都要受影响。现在,掉链子的是Model 3未能起量。
未来一片光明现在看来,特斯拉在2018年遇到的一切困境,都源于 2016 年 5 月的激进规划。如果没有 Dreadnought,也就不会有这么多困难和挑战出现了。
有人会说,在传统车企纷纷觉醒的今天,特斯拉失去的不仅是高管和几十亿美元,2018年未能实现 50 万辆/年的产能,以及与之匹配的其他业务进展,丢掉的空窗期才是最大的损失。
对于这个说法,我想贴Elon的传记《硅谷钢铁侠》中的一段话。
别忘了,特斯拉最初的计划是 2020 年实现 50 万辆/年的产能,虽然2018年最终未能实现,但即便推迟到 2019 年,也比原计划提前了整整一年。
现在看来,特斯拉在2018年遇到的一切困境,都源于 2016 年 5 月的激进规划。如果没有 Dreadnought,也就不会有这么多困难和挑战出现了。
有人会说,在传统车企纷纷觉醒的今天,特斯拉失去的不仅是高管和几十亿美元,2018年未能实现 50 万辆/年的产能,以及与之匹配的其他业务进展,丢掉的空窗期才是最大的损失。
对于这个说法,我想贴Elon的传记《硅谷钢铁侠》中的一段话。
别忘了,特斯拉最初的计划是 2020 年实现 50 万辆/年的产能,虽然2018年最终未能实现,但即便推迟到 2019 年,也比原计划提前了整整一年。